One to pack them all
Orkla Confectionery & Snacks responds to new case packing demands with highly flexible Syntegon equipment
Among the many factors of success, adapting to market changes is probably the most vital. In this regard, Orkla Confectionary & Snacks took a decisive step to stay abreast of competition. The Finnish confectionery producer decided to tweak its secondary packaging to meet international export requirements. With Syntegon’s Elematic 3001 WA Compact, a flexible and modular case packing solution, Orkla is securing its competitiveness.
Whether sweet or salty, liquorice is highly popular throughout Scandinavia. The company Orkla Confectionary & Snacks Finland AB belongs to the Oslo-based Orkla Group, which comprises a wealth of consumer goods companies and totals 70 brands for chocolate and liquorice. The Panda brand is a mainstay in the portfolio and is the market leader for Finnish liquorice and known for its countless varieties since 1927. With its tasty liquorice creations, Orkla Confectionery & Snacks mainly targets the markets in Scandinavia, the UK, the US and Canada, and Central Europe.
Changing export conditions
Having multiple export countries means different packaging requirements. Due to changing transport conditions in the US and Canada, Orkla had to switch from packing two products side-by-side to packs in a row while increasing the production capacity. To save space, a new case packer should be compact and able to handle ten different case formats, while operating at double the speed compared to the previous case packer. Quick changeover times are required to efficiently switch between the different formats.
Flexible and compact
When Orkla heard about Syntegon and the Elematic 3001 WA Compact, they were thrilled: the machine seemed to be the perfect fit for packing a broad variety of bag sizes into different case formats. “After the first presentation, it was obvious that the machine delivers what its name suggests – a compact, easy-to-clean and accessible case packer,” Arto Liimatainen adds. One thing in particular caught the manager’s attention: the case packer’s format flexibility and speed.
The Elematic at Orkla can handle ten case formats at an infeed rate of around 150 bags per minute. Thanks to the machine’s modularity, the operators can easily adapt the collating chain for the next case format. Moreover, Syntegon kept the overall number of format parts to a strict minimum for a time-saving format changeover. “The machine’s unmatched flexibility tipped the scales for Syntegon, but so did the company’s service support,” Jari Leinonen explains.
Packaging design at its best
Orkla relies on ten case formats to pack different counts of bags standing upright in rows. “However, it quickly became clear that one of the formats could not be processed on the Elematic,” explains Bernhard Vaihinger, product manager for case packers at Syntegon. “We then redesigned the format and shared our proposal, together with explanatory videos on “How to handle the case” with the customer.” It was important to keep the blank’s dimensions and to ensure that the full wrap-around case with perforation remained feasible and the case easy to open.
“We were impressed with the fast and efficient solution from Syntegon,” says
Arto Liimatainen. “In total, we are now able to pack ten case formats with different
bag configurations, including 2 times 6 bags, 3 times 6 or even 1 times 8.” Thanks to
its case flexibility, the Elematic 3001 WA Compact can produce full wrap-around,
ledge tray and tray cases for various applications.
Building around bags
Because the bags do not have a fixed, stable shape, they posed another challenge Syntegon was willing to take on. Case forming, placing the bags inside and closing the bag thus required gentle handling and accurate grouping to literally “build” the case around the bags, that beneficial is for the Elematic 3001 WA Compact. The Elematic currently runs every day and is changed to a new format twice a day on average.
Leaner processes
Thanks to the new machine, Orkla was able to revamp its production line without having to expand its footprint. “We are very pleased to have secured our competitiveness with a much leaner set-up,” says Arto Liimatainen. “This fruitful cooperation has not only benefitted our production. We also built a strong bond with Syntegon which we are eager to maintain for many years to come.”
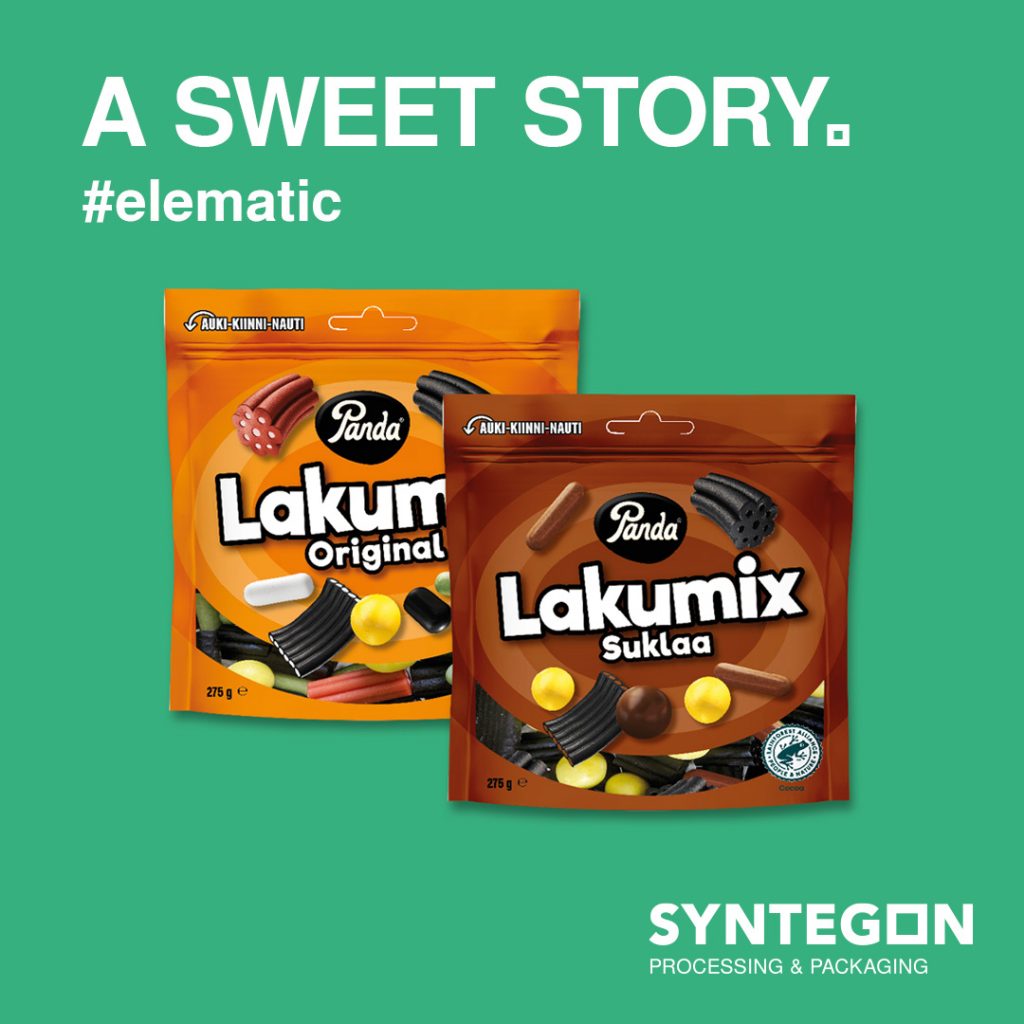
The Panda brand is well-known in Scandinavia and beyond.
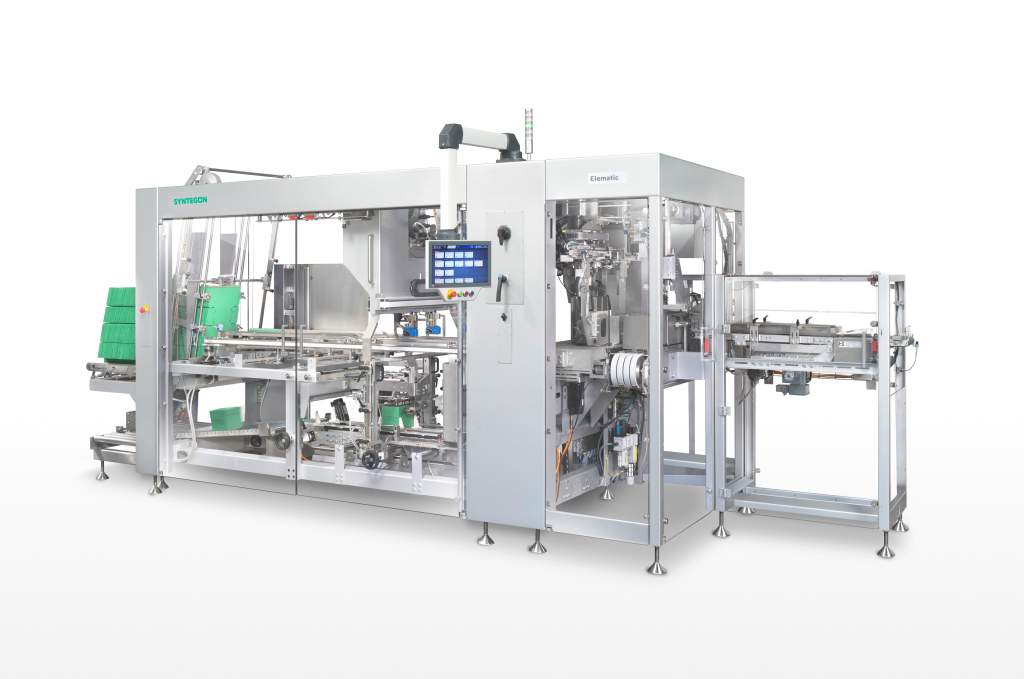
The Elematic 3001 WA Compact achieves cases with a wealth of bag configurations
About Syntegon
Processing and packaging for a better life – this is what 5,800 Syntegon employees work for every day. Syntegon, headquartered in Waiblingen, Germany, with over 160 years of experience, specializes in processing and packaging for the global pharmaceutical and food industries. Achieving 1.4 billion EUR in annual sales in 2022, the company focuses on safe and high-quality technologies for pharma and food industry. As a leader in sustainable packaging, Syntegon operates across 30 sites globally, actively working to reduce energy consumption and lower emissions.
Here you can download the success story.