Handling cheese blocks right with Piab’s vacuum technology
Packaging cheese blocks vacuum-wrapped in film represents a major challenge for process automation. With the help of Piab’s piGRIP® configurable suction cups and high-performance vacuum ejectors, the machine and plant manufacturer TGW Robotics GmbH has developed a gripper that ensures a stable process.
When the slice of cheese is on the breakfast roll in the morning, it has already completed a considerable number of process steps. One of these is the packaging of the ready-to-sell blocks of cheese for the wholesale and retail outlets.
TGW Robotics, a subsidiary of the TGW Logistics Group with headquarters in Wels, Austria, specializes in the construction of conveyor technology, palletizing and depalletizing systems. With 100 employees in Stephanskirchen near Rosenheim, external customers are served in addition to systems for the parent company’s logistics centres.
Mature cheese blocks of up to 25kg arrive at the beginning of the process in a ripening box on a pallet using a roller conveyor. The box is removed with a mechanical gripper and the stacked cheese is transferred from wooden to plastic pallets and held in a clean or white room. The cheese will eventually be cut into slices or grated depending on customer requirements, but each block needs to be checked prior to this.
The large blocks of cheese should arrive shrink-wrapped and vacuum-packed and, depending on the time this wrapping process took place, the film may have become wrinkled or the film may not have been completely sealed. These scenarios can present a major challenge in automating a vacuum handling system as there is the potential for the blocks of cheese to be dropped during transfer due to leaking air unless the gripper system can compensate for these potential issues.
This means that the performance of suction cups and vacuum pumps are vital to ensuring the automatic handling of the cheese blocks continue without any problems while ensuring the vacuum lifting process itself does not cause damage to the packaging, which can lead to product spoilage. At the same time, the size and weight of the vacuum ejectors must be small enough to integrate directly on the gripper. Today, the need to reduce energy consumption is a major focus and is best met with Piab’s low-energy three-stage COAX® technology.
Before the blocks can continue to the final processing stage, the integrity of the film on each block needs to be checked. TGW integrated a Kenos® surface gripper to carry out a preliminary check to ensure the film is properly sealed around the block of cheese. In this step, if the cheese can be lifted using the Kenos® gripper from Piab, the block of cheese moves on to the final process and is palletized using the TGW gripper. If the block of cheese cannot be lifted it is automatically rejected.
The grippers developed by TGW include Piab’s configurable piGRIP® suction cups with a lip that was originally developed for handling soft plastic pouches such as crisp bags, and a high-performance vacuum pump based on Piab’s patented COAX® technology for multi-stage ejectors.
Maximilian Schaletzky, construction engineer at TGW explains, “The piGRIP suction cups are fantastic for our application because the soft lip can wrap around any curvature of the film. So, they can hold the blocks of cheese safely.“
“We chose to work with Piab because they were able to put together exactly the suction cups and vacuum systems that fulfil all tasks and requirements from their broad portfolio. Accordingly, we can supply our customers with an excellent system for the automated handling of blocks of cheese”, continues Schaletzky.
Sebastian Liebetrau, Team Leader Robotic Gripping Sales, Germany, and the Piab specialist on site at TGW explains: “In such complex cases, we as experts in the field of gripping and lifting make a pre-selection from our extensive portfolio and then carry out trials at the customer’s site to find the best possible solution.“
The gripper also includes additional suction cups on level compensators, which place paper layers between the individual layers of cheese blocks as part of the packaging. This automation means there is no need for an operator to manually place this layer, removing any potential repetitive strain injuries as well as ensuring the whole process is efficient and automated.
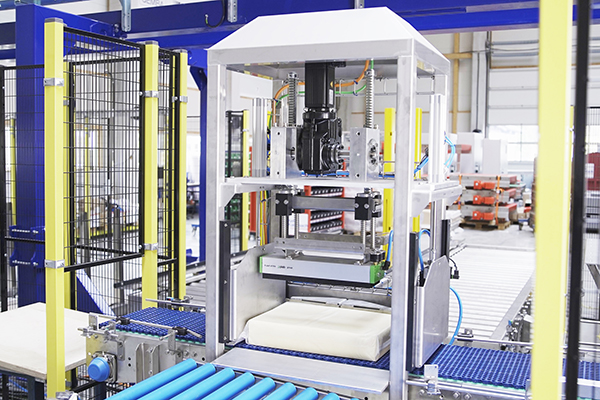
The vacuum packaging is checked with Piab’s Kenos® area gripper.
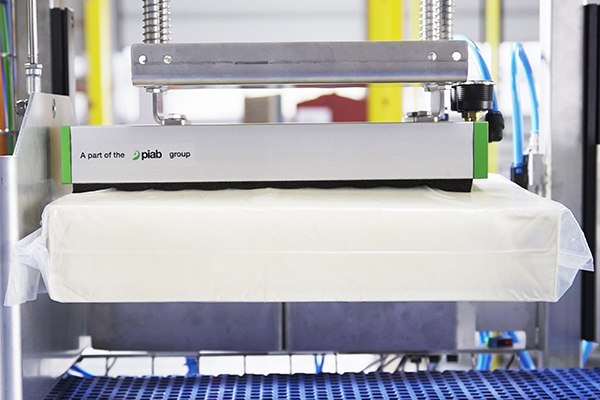
If the block of cheese can be lifted, the signal of the photoelectric sensor can show-up under the cheese and the system sorts the cheese into the good batch.
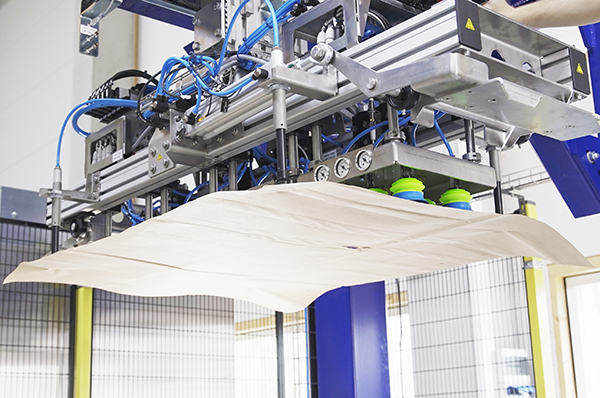
The automatic picking up and placing of the intermediate paper liner is a great relief for the employees.
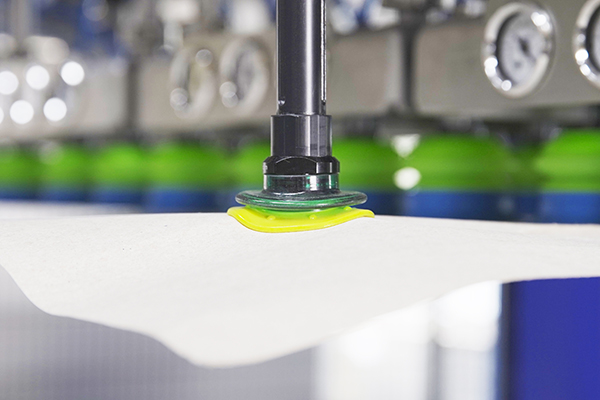
Piab’s DURAFLEX® BX suction cups easily hold air-permeable cardboard. The soft lip adapts to the material.
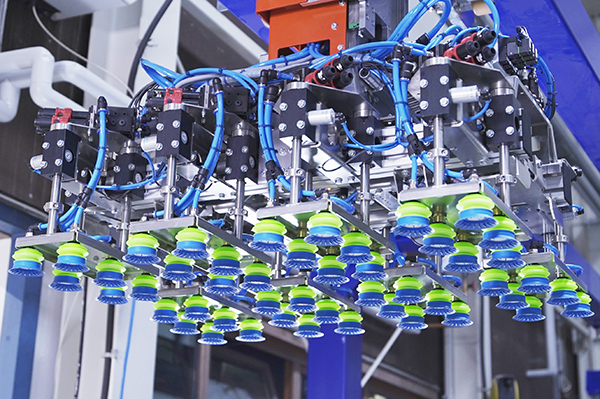
Piab’s configurable piGRIP® suction cups are specially designed to hold uneven bags and vacuum packaging.
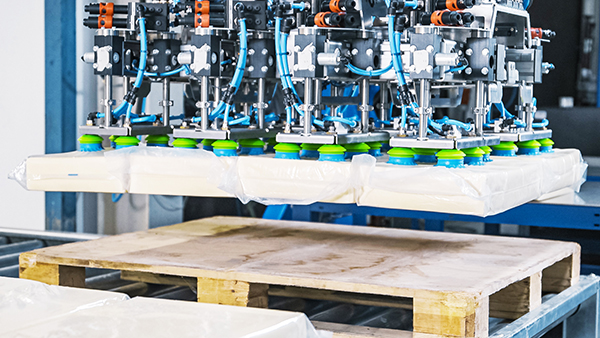
With the TGW gripper, eight blocks of cheese can be picked up simultaneously by Piab’s piGRIP® suction cups.
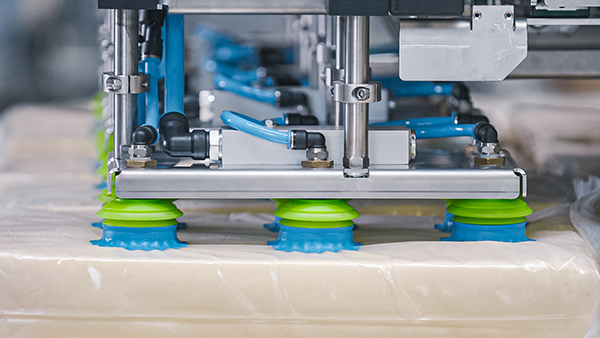
Piab’s piGRIP® suction cups with their soft lip specially designed for handling bags and vacuumed products adapt perfectly to the surface properties of the film in which the cheese is packaged.